Step by step journey of your tea package
Hanna VillbergIt is funny to see the faces of people when they hear about all the processes that we go through just to get the teas to our customers. It is best understood when they come to visit us on the spot – we go to see the plantation, we have a tour in our factory and go through the process of making tea and the steps that take place after the tea is done. We taste some teas and talk about life in Georgia and in the end, in most of the cases, people are surprised about how many steps it actually takes to get the leaves from the fields to their cup at home.
Let’s be honest – we are freaks. It seems that we have some trust issues and we like to do everything ourselves. We do find ourselves being frustrated sometimes but we also find ourselves laughing over our “Monk disease” that everything should be perfectly perfect. But this makes it us and we cannot help it.
I put down a list of things that take place before a customer gets their tea package. A step by step journey from plucking to unpacking the delivery from the Renegade Tea farmers.
1. TEA LEAVES TO THE FACTORY
Getting freshly plucked leaves to the factory is crucial. The natural oxidation process starts right after the leaves are taken from the bush. The leaves are plucked into bamboo baskets to get the airflow going to slow the process of oxidation. For example, we usually do not use leaves from Mandikori Estate for green tea because the plantation is located almost an hour away from the factory and by the end of the plucking day, they would be more naturally oxidized than we would prefer for making a proper green tea. We gather the leaves and bring them to the factory twice a day, just to keep the raw material as good as possible.
Kristiina bringing fresh leaves to the factory.
2. TEA MAKING
When leaves get to the factory, it is time for Hannes and Tomas to do their magic. We do have a production plan and the idea of teas and quantities that we would like to make but there are also some “unknowns” that dictate the “tea making plan”. Like weather conditions, for example, some teas just need certain weather to bring out the right characteristics. So besides the rest of the team, the weather forecast is also a partner to Hannes and Tomas :)
3. SORTING TEAS
When the tea is ready, it goes straight to sorting. We do look over every batch of tea that we make and we do it manually, just to make sure that there are no parts that do not belong to the tea package. For example, leaves which haven’t rolled during the process or parts of weeds that have accidentally found their way into the bamboo basket while plucking.
4. CHECKING HUMIDITY LEVELS OF TEAS
Even though all the teas go to the dryer as a last step of the process, we do double-check the humidity levels just to make sure that there wouldn’t be surprises while opening the package sometime later. Humidity levels in the package should be close to zero to prevent the life on funguses and mould, hence why we weigh, dry the tea, and weigh it again and we run this through with every batch of tea we make. We must do this to ensure the safety of each batch.
5. TASTING TEAS
We need to admit that it is just not physically possible to enjoy a cup of tea every day, just because we taste a lot of teas and usually there is just no room in the system to enjoy a full cup. We taste all the batches of teas that we make, just to make sure that the right characteristics are in place. When we produce tea after already developed recipes, we do know what we are looking for. But sometimes weather, plucking quality and other unknown factors play tricks on us and the outcome has a whole new taste profile. In this case, this batch will end up as a separate tea, with a new name and a story. There have been days when we have tasted close to 20 different batches of black teas... Can you even imagine that? You can also see one of our tasting sessions from the past season and arguments over naming the teas HERE or read about the whole tasting process HERE.
Tea tasting session.
6. TEAS AND GIVING THEM A STORY
We often get asked about the names of our teas and stories that are written to the packages. It is fairly simple (but not always). In some cases Hannes and Tomas have already some story in the back of their mind during the making process, in some cases, teas just remind us something, for example, Kartuli Alphabet – the looks of the leaves reminded us the alphabet of the Georgian language. Green Velvet got its name by its velvety leaves and Shit Long, well... this tea just looked quite crappy but tasted too good and we didn’t want to waste it.
7. DESIGNING LABELS FOR THE PACKAGES
We make all the labels ourselves as well. Meaning that we design them, we create the stories, we print them. Mostly the one who is behind making the labels is Mario. He prepares all the printing files while tea masters and team marketing aka me, Kristiina, and Miina take care of the content.
8. PRINTING THE LABELS
This is a really sensitive subject for us, especially for Mario but this year also for Kristiina who needed to take over the packaging department due to the covid crisis. So what’s up with that you may ask? Well, last year we were joking that Mario has spent more time with the printer than with Kendrick (our son). Just to say that there were days when we got only 1 perfectly printed label out from the machine. You need to give some love and patience to the printer otherwise it will screw you. As we do have personalized labels and every batch has a different one (batch number, plantation, harvest info), then we cannot buy in ready-made labels. If you know anything about label printers, then you also probably know that it is hard to find a perfectly working tool. Luckily, we are going to get a new printer soon, hopefully, this one wouldn’t be so fretful.
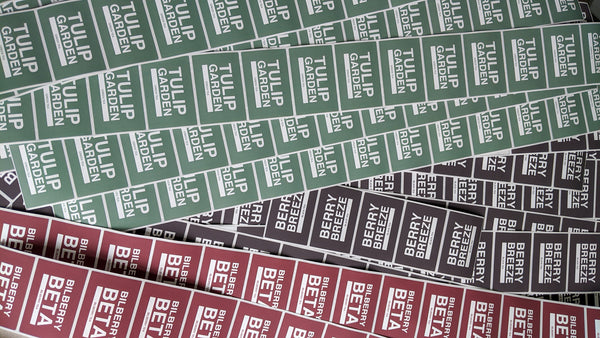
9. MAINTAINING OUR PRINTER
As just mentioned above, we do spend a lot of time with the printer. We also haven’t found the company in Georgia who offers maintenance for it, so we do it ourselves and off-season we bring it to Estonia. It is like a small spa treatment for the printer when it gets touched by the pros.
Mario doing maintenance for the printer.
10. STICKING LABELS TO THE PACKAGES
A perfect thing to do when you get overwhelmed by the “surprises” and casual farming problems. Each package needs 2 labels, so there is always something to stick if the printer hasn’t started to protest.
11. PACKAGING
Each package, packaged manually, scaled one by one. Also, a pretty calming process but takes loads of time.
Ana and Eteri packaging teas of season nr 3.
12. ORGANIZING TRANSPORTATION TO ESTONIA
Another sensitive subject, especially again for Mario, who is organizing the logistics. We send our teas from Georgia to Estonia just to avoid additional hustle with taxes and customs procedures that our customers would have if we would send teas out straight from Georgia, as Georgia does not belong to the EU. But what is sensitive about the topic is the fact that finding a reliable partner who would carry our teas to Estonia hasn’t been successful yet. Mostly because of the quantities that we are producing at the moment. It wouldn’t be a problem if we would have quantities that would cover the whole truck, but as we are still waiting for our plantations to mature and get the production levels up, we are in constant headache to find reasonable ways to deliver our goods. Just to mention, air freight is always an option but producing organic tea which is already costly, and then to add a rather high rate for transportation… Adds up to a really pricy tea. We are aiming to be affordable for a wide audience by offering pure chemical-free tea straight from the farmer.
13. PUTTING TOGETHER THE ORDERS
When tea arrives to Estonia, Priit is giving it a big warm welcome. He is the guy whose home is a warehouse. He assembles all the orders and sends them out. So if anything is messed up with your order, you can most likely blame Priit for it. But I am sure that this wasn’t intentional and mistakes can happen from time to time, he is still giving his best as we all do :)
Don't you worry - Priit is "tasting" only his own tea packages :)
14. TEA REACHES THE CUSTOMER
Well, hello new or already familiar customer! :) As an entrepreneur selling a physical product, it is probably the most exciting part. It is a shame that in most cases we cannot see the emotion when people unpack their orders. But luckily we still receive some feedback letters or social media posts – it makes us happy :)
With everything being said, we still enjoy our lives as tea farmers even though it is 180 degrees from what we did in the past. We have bad days and we have good ones but luckily we have managed to balance each other and also learned how to take things more in the “Georgian way” - not to worry constantly about everything and take it easier.
Written by Hanna